From metal powder to jet engine
Das Thema des Monats
Since January 2018, we have been presenting an exciting topic in the field of materials science every month.
The “topic of the month” is explained in a simple and understandable way and provides informative insights into the research activities of our department.
The topic of the month in August comes from the Institute of Materials Science and Engineering for Metals (WW2) and has the title:
From metal powder to jet engine
by Julian Pistor
Worum geht es bei dem Thema?
In dem Projekt geht es um die elektronenstrahlbasierte additive Fertigung von einkristallinen Nickel-Basis Superlegierungen für Turbinenschaufeln in Flugzeugtriebwerken oder stationären Gasturbinen. Das Projekt ist angesiedelt im Sonderforschungsbereich SFB/TR 103 „Vom Atom zur Turbinenschaufel – Wissenschaftliche Grundlagen für eine neue Generation einkristalliner Superlegierungen“.
Kurz gesagt, es geht um 3D‑Druck von Metallen, die in Flugzeugturbinen eingesetzt werden.
Jeder Flugzeugpassagier hat in der Regel großes Interesse daran, den Weg aus Reiseflughöhe zum Boden sicher hinter sich zu bringen. Es ist allgemein bekannt, dass dies mit einem funktionierenden Triebwerk wahrscheinlicher ist – es sollte also möglichst nicht versagen. Daher sind die Anforderungen an die Triebwerksmaterialien natürlich hoch.
Da die additive Fertigung (3D‑Druck) noch relativ jung ist, ist es bisher nicht gelungen, ein ausreichend gutes Verständnis darüber zu erlangen, wie solch sicherheitsrelevante Bauteile erzeugt werden können. Diese benötigen in den heißesten Bereichen nämlich eine besondere (Kristall-) Struktur: Sie müssen einkristallin sein.
Aber was muss man sich darunter vorstellen? Wenn man ein Metall aus der Schmelze erstarren lässt, muss die Erstarrung irgendwo beginnen. Dies geschieht in Form von kleinen Bereichen, sog. Keimen, die dann anfangen zu wachsen und letztendlich dazu führen, dass das gesamte Material erstarrt. Diese Keime stoßen beim Wachsen aufeinander und bilden Grenzregionen, sog. Korngrenzen. Das entstandene Gefüge nennt sich Polykristallin. Diese Korngrenzen haben im niedrigen Temperaturbereich durchaus einen positiven Effekt auf die mechanischen Eigenschaften eines Metalls. Jedoch nicht bei hohen Temperaturen, da hier zeitabhängige plastische Verformung (Kriechen) der maßgebliche Schädigungsprozess ist und dies bei Korngrenzen schneller abläuft. Daher sind bei Hochtemperaturanwendungen Werkstoffe mit Korngrenzen weniger geeignet, und es kommen (technische) Einkristalle zum Einsatz, die nur aus einem Korn bestehen. Wie man solche Strukturen additiv definiert herstellen kann und welche Eigenschaften die additiv gefertigten Einkristalle im Vergleich zu gegossenen Einkristallen haben, ist Hauptgegenstand dieses Projektes.
Wo findet es Anwendung?
Bisher werden einkristalline Nickel-Legierungen nicht additiv, sondern über das Gießen in eine Form hergestellt. Dieser Prozess ist langsam und sehr begrenzt in der Komplexität der Gussbauteile. Außerdem sind die Bauteile nach dem Gießen nicht sofort einsatzfähig, sondern müssen aufwändig bei sehr hoher Temperatur für lange Zeiten von bis zu 20 Stunden geglüht werden. Durch die additive Fertigung kann auf eine Form wie beim Gießen verzichtet werden und die Geometriekomplexität ist dadurch nahezu unbegrenzt. Eine Wärmebehandlung danach ist nach wie vor nötig, jedoch in nur einer Stunde erledigt. Es können damit neue Generationen von effizienteren Turbinen entwickelt werden.
Was ist weiter geplant?
Es ist uns als erste Forschungsgruppe bereits gelungen, einkristalline Zylinder und Blöcke additiv zu bauen (Abbildung 1).

An diesen konnten wir nachweisen, dass die Eigenschaften besser als bei gegossenen Einkristallen sind. Leider haben wir eine „Schale“ von feinen Körnern, die unseren Einkristall-Kern umgibt. Diese muss prozesstechnisch vermindert werden. Außerdem arbeiten wir daran, komplexe Geometrien, wie sie in Turbinen vorkommen zu realisieren (Abbildung 2). Dabei sind wir auf einem guten Weg.
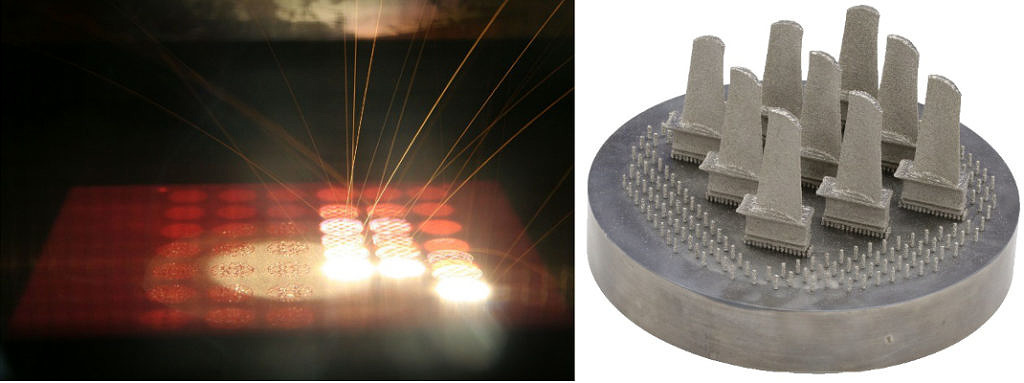
Zur Person:
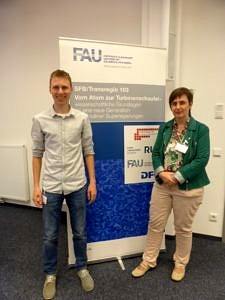
Name: Julian Pistor
Studium: Materialwissenschaft und Werkstofftechnik M.Sc.
Position: Wissenschaftlicher Mitarbeiter
Forschungsschwerpunkt: Elektronenstrahlbasierte additive Fertigung, Ni-Basis Superlegierungen
Hobbys: Musik, Triathlon