Arc-based additive manufacturing of large-volume structural parts for aviation
Since January 2018, we have been presenting an exciting topic in the field of materials science every month.
The “topic of the month” is explained in a simple and understandable way and provides informative insights into the research activities of our department.
The topic of the month in May comes from the Institute of General Materials Properties (WW1) and has the title:
Arc-based additive manufacturing of large-volume structural parts for aviation
by Daniel Elitzer
Worum geht es bei dem Thema?
Im Rahmen des vom BMWi-geförderten Verbundprojekts Regulus beschäftigen wir uns am Lehrstuhl WW1 mit der Entwicklung eines neuen Prozesses, mit dem großvolumige Titan-Luftfahrtbauteile per drahtbasierter Lichtbogentechnologie dreidimensional aufgebaut werden können. Dies geschieht in Zusammenarbeit mit der TU München und den Firmen Aircraft Philipp, Heggemann, Software Factory und Fronius. Abbildung 1 zeigt den Roboter, mit dem die Parameterstudien an der TUM durchgeführt werden und das Probenmaterial erzeugt wird.
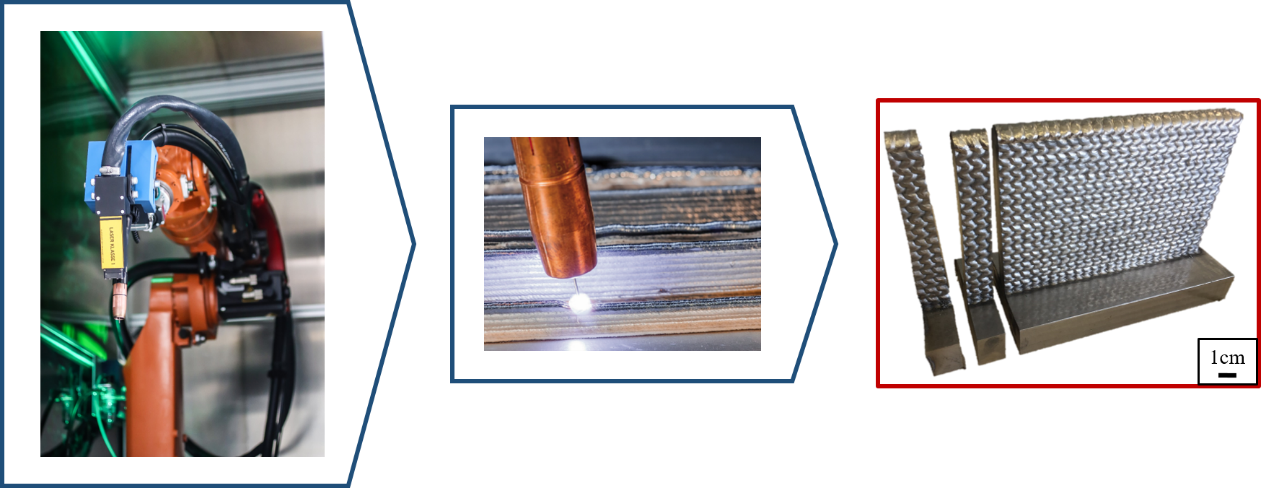
Dabei wird ein Schweißprozess auf Basis des Metall-Inertgas-Lichtbogenschweißens, dem sogenannten Cold Metal Transfer (CMT) – Verfahren verwendet. Abbildung 2 stellt schematisch den Ablauf dar.
Dadurch entstehen neben der verringerten Wärmeeinbringung weitere Vorteile, wie ein stabilerer Lichtbogen und höhere Auftragsraten von bis zu 5 kg/h.
Durch genaue Kontrolle der Prozessparameter können so Nähte gezogen werden, auf die durch das Anheben des Schweißbrenners additiv aufgebaut werden kann. So entstehen innerhalb kürzester Zeit endkonturnahe Bauteile.
Wo findet es Anwendung?
Im Bereich der Luft- und Raumfahrt ist die Legierung Ti-6Al-4V mit mehr als 50 % die am meisten verwendete Titanlegierung. Durch die hohe Festigkeit in Verbindung mit der geringen Dichte kann es anstatt von Stahl, Nickelbasissuperlegierungen und Aluminiumlegierungen eingesetzt werden.
Typische Strukturbauteile aus Ti-6Al-4V werden häufig in schwer belasteten Bereichen des Flugzeugs, z.B. als Türrahmen oder Turbinenhalterung eingesetzt. Ein solches Strukturbauteil ist in Abbildung 3 zu sehen.
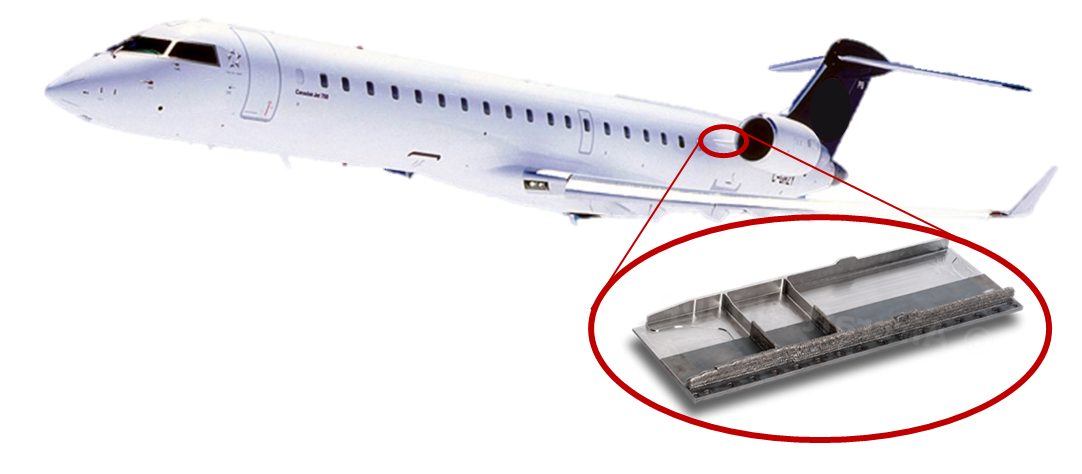
Das derzeitige Produktionsverfahren basiert auf dem Fräsen von massiven Metallblöcken. Diese konventionelle Methode bringt einige Herausforderung mit sich, wie einem hohen Werkzeugverschleiß, Bearbeitungszeit aber vor allem dem kostenintensiven hohen Materialverbrauch. Aktuell beläuft sich dieses sogenannte Buy-to-Fly Verhältnis auf 25:1, d.h. es werden bis zu 96% des Ausgangsmaterials zerspant.
Mit dem CMT-Verfahren ist es nun möglich, dieses Verhältnis auf 5:1 zu senken. Durch die Umstellung auf die additive Fertigung mittels drahtbasierter Lichtbogentechnologie ist es zudem möglich, im Gegensatz zu SLM- oder EBM-Prozessen, mit signifikant höheren Auftragsraten und Stückzahlen zu produzieren.
Um ein zertifiziertes Verfahren zu erhalten, ist es deshalb wichtig, den Prozess hinsichtlich der mikrostrukturellen Entwicklung im Schmelzprozess zu analysieren, daraus Optimierungsmaßnahmen abzuleiten und somit das mechanische Eigenschaftsprofil so zu optimieren, dass ein ermüdungsfestes Klasse 1 Bauteil entsteht.
Was ist weiter geplant?
In dem vom Deutschen Zentrum für Luft- und Raumfahrt (DLR) geförderten LuFo V-3 Projekts steht aktuell die Untersuchung der Parameter/Mikrostruktur-Wechselwirkungen im Vordergrund. So wird auch durch quasistatische und zyklische Versuche ein Prozessfenster entwickelt, mit dem stabil und innerhalb kürzester Zeit endkonturnahe Strukturteile gefertigt werden können. Des Weiteren werden auch Wärmebehandlungsstrategien untersucht, mit denen der Werkstoff noch genauer dem Anforderungsprofil angepasst werden kann.
Zu den Personen:
Für die Durchführung und Koordination der mikrostrukturellen Analysen und der Untersuchung der mechanischen Eigenschaften im Bereich des 3D-Schweißens ist Daniel Elitzer (Mitte) verantwortlich.
Nach dem Studium der Materialwissenschaften und Werkstofftechnik (M.Sc.) arbeitet er als wissenschaftlicher Mitarbeiter am Lehrstuhl WW1 in der Arbeitsgruppe von PD Dr. Höppel.
Mitwirkende (v.l.):
Stefanie Jäger, Max Bader, Florens Bach (Abschlussarbeiter)
Clara Höll, Phillipp Schultheiß, Benedict Ott (HiWi’s)